Ultrasound
- Andi Thoncianus
- Mar 8, 2018
- 6 min read
You often hear people using the phrase "as blind as a bat"—but if bats could talk, would they criticize us for being "as deaf as a human"? We may think we're good at hearing things but our ears can detect only a relatively narrow band of frequencies (sounds of different pitch) centered on the human voice—the sound we most need to hear. Bats, moths, dolphins, and various other creatures can hear much higher frequencies of sound beyond the range of human hearing, which is known as ultrasound. Since scientists discovered ultrasound, they have found all kinds of important uses for it, from medical diagnosis to materials testing and scientific research. Let's take a closer look at ultrasound and how it works.
What is Ultrasound?
Human ears can hear sound waves that vibrate in the range from about 20 times a second (a deep rumbling noise) to about 20,000 times a second (a high-pitched whistling). Children can generally hear higher-pitched sounds than their parents, because our ability to hear high frequencies gets worse as we get older.) Speaking more scientifically, we could say that the sounds we can perceive have a frequency ranging from 20–20,000 hertz (Hz). A hertz is a measurement of how often something vibrates and 1 Hz is equal to one vibration each second. The human voice makes sounds ranging from a few hundred hertz to a few thousand hertz.
Suppose you could somehow hit a drum-skin so often that it vibrated more than 20,000 times per second. You might be able to see the skin vibrating (just), but you certainly couldn't hear it. No matter how hard you hit the drum, you wouldn't hear a sound. The drum would still be transmitting sound waves, but your ears wouldn't be able to recognize them. Bats, dogs, dolphins, and moths might well hear them, however. Sounds this like, with frequencies beyond the range of human hearing, are examples of ultrasound.
Ultrasound is defined by the American National Standards Institute as "sound at frequencies greater than 20 kHz." In air at atmospheric pressure ultrasonic waves have wavelengths of 1.9 cm or less.
Ultrasound waves have higher frequencies than normal sound waves, but they also have shorter wavelengths. In other words, the distance between one ultrasound wave traveling through the air and the one following on behind it is much shorter than in a normal sound wave. This has an important practical effect: ultrasound waves reflect back from things much better than ordinary sound waves, and that makes them very useful indeed.
Ultrasound is used in many different fields. Ultrasonic devices are used to detect objects and measure distances. Ultrasound imaging or sonography is often used in medicine. In the nondestructive testing of products and structures, ultrasound is used to detect invisible flaws. Industrially, ultrasound is used for cleaning, mixing, and to accelerate chemical processes. Animals such as bats and porpoises use ultrasound for locating prey and obstacles. Scientist are also studying ultrasound using graphene diaphragms as a method of communication. A common ultrasound application is an automatic door opener, where an ultrasonic sensor detects a person's approach and opens the door. Ultrasonic sensors are also used to detect intruders; the ultrasound can cover a wide area from a single point. The flow in pipes or open channels can be measured by ultrasonic flowmeters, which measure the average velocity of flowing liquid. In rheology, an acoustic rheometer relies on the principle of ultrasound. In fluid mechanics, fluid flow can be measured using an ultrasonic flow meter.

How is Ultrasound Made?
It's impossible for us to make ultrasound the same way we make normal sounds—by hitting and blowing things, as we do, for example, in musical instruments. That's because we can't hit and blow things fast enough. But we can make ultrasound using electrical equipment that vibrates with an extremely high frequency. Crystals of some materials (such as quartz) vibrate very fast when you pass electricity through them—an effect called piezoelectricity. As they vibrate, they push and pull the air around them, producing ultrasound waves. Devices that produce ultrasound waves using piezoelectricity are known as piezoelectric transducers. Piezoelectric crystals also work in the reverse way: if ultrasound waves traveling through the air happen to collide with a piezoelectric crystal, they squeeze its surface very slightly, causing a brief burst of electricity to flow through it. So, if you wire up a piezoelectric crystal to an electric meter, you get an instant ultrasound detector.
Ultrasound waves can be produced using magnetism instead of electricity. Just as piezoelectric crystals produce ultrasound waves in response to electricity, so there are other crystals that make ultrasound in response to magnetism. These are called magnetostrictive crystals and the transducers that use them are called magnetostrictive transducers. (The magnetive effect is known as magnetostriction.)
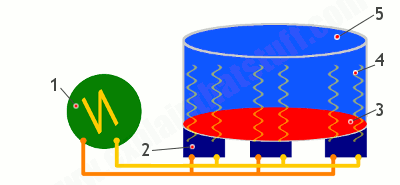
How ultrasound is made for cleaning things.
1) A high-frequency alternating electricity supply sends power to three piezoelectric transducers
2). These jiggle about at ultrasonic frequencies, sending their vibrations to a thin, quartz glass plate
3), which transmits waves
4) into a basin filled with fluid
5) into which you place the objects to be cleaned.
Ultrasound Application for Processing
Ultrasonication offers great potential in the processing of liquids and slurries, by improving the mixing and chemical reactions in various applications and industries. Ultrasonication generates alternating low-pressure and high-pressure waves in liquids, leading to the formation and violent collapse of small vacuum bubbles. This phenomenon is termed cavitation and causes high speed impinging liquid jets and strong hydrodynamic shear-forces. These effects are used for the deagglomeration and milling of micrometre and nanometre-size materials as well as for the disintegration of cells or the mixing of reactants. In this aspect, ultrasonication is an alternative to high-speed mixers and agitator bead mills. Ultrasonic foils under the moving wire in a paper machine will use the shock waves from the imploding bubbles to distribute the cellulose fibres more uniformly in the produced paper web, which will make a stronger paper with more even surfaces. Furthermore, chemical reactions benefit from the free radicals created by the cavitation as well as from the energy input and the material transfer through boundary layers. For many processes, this sonochemical effect leads to a substantial reduction in the reaction time, like in the transesterification of oil into biodiesel.
Substantial ultrasonic intensity and high ultrasonic vibration amplitudes are required for many processing applications, such as nano-crystallization, nano-emulsification,[40] deagglomeration, extraction, cell disruption, as well as many others. Commonly, a process is first tested on a laboratory scale to prove feasibility and establish some of the required ultrasonic exposure parameters. After this phase is complete, the process is transferred to a pilot (bench) scale for flow-through pre-production optimization and then to an industrial scale for continuous production. During these scale-up steps, it is essential to make sure that all local exposure conditions (ultrasonic amplitude, cavitation intensity, time spent in the active cavitation zone, etc.) stay the same. If this condition is met, the quality of the final product remains at the optimized level, while the productivity is increased by a predictable "scale-up factor". The productivity increase results from the fact that laboratory, bench and industrial-scale ultrasonic processor systems incorporate progressively larger ultrasonic horns, able to generate progressively larger high-intensity cavitation zones and, therefore, to process more material per unit of time. This is called "direct scalability". It is important to point out that increasing the power of the ultrasonic processor alone does not result in direct scalability, since it may be (and frequently is) accompanied by a reduction in the ultrasonic amplitude and cavitation intensity. During direct scale-up, all processing conditions must be maintained, while the power rating of the equipment is increased in order to enable the operation of a larger ultrasonic horn.
Ultrasonic cleaners, sometimes mistakenly called supersonic cleaners, are used at frequencies from 20 to 40 kHz for jewellery, lenses and other optical parts, watches, dental instruments, surgical instruments, diving regulators and industrial parts. An ultrasonic cleaner works mostly by energy released from the collapse of millions of microscopic cavitations near the dirty surface. The bubbles made by cavitation collapse forming tiny jets directed at the surface.
Similar to ultrasonic cleaning, biological cells including bacteria can be disintegrated. High power ultrasound produces cavitation that facilitates particle disintegration or reactions. This has uses in biological science for analytical or chemical purposes (sonication and sonoporation) and in killing bacteria in sewage. High power ultrasound can disintegrate corn slurry and enhance liquefaction and saccharification for higher ethanol yield in dry corn milling plants.

Schematic of bench and industrial-scale ultrasonic liquid processors
Warning :
Occupational exposure to ultrasound in excess of 120 dB may lead to hearing loss. Exposure in excess of 155 dB may produce heating effects that are harmful to the human body, and it has been calculated that exposures above 180 dB may lead to death.
Comments