Palm Oil Refining
- Andi Thoncianus
- Mar 11, 2018
- 5 min read
In order to get the pure and refined oil, there are three main process in chemical palm oil refinery plant and chemical palm kernel oil refinery plant : degumming process, bleaching process and deodorising process.
The Purpose of Palm Oil Refining : Palm Oil refining process refers to a series of refining processes that can remove phospholipids, FFA, pigment, off-flavor and other impurities in the palm oil. Palm oil refining process or vegetable oil refinery is essential to ensure removal of gums, waxes, phosphatides and free fatty acid (F. F.A.) from the edible oil. To impart uniform color by removal of coloring pigments and to get rid of unpleasant smell from the palm oil by removal of odiferous matter.
Degumming process : The Oil is heated under vaccum and phosporic acid is added to separate the gums, which are impurities that will be removed in the belaching process. Through phosphoric acid application, the fatty acid and gum contained in the palm oil and palm kernel oil will be separated from foreign impurities, like trace minerals, iron, cooper and other. This process offers necessary preparation for the next chemical refining process.
Bleaching process : Add bleaching earth (active clay) to absorb all colour in the oil. It adopts vacuum system to remove the impurities and color pigments from the crude palm oil and crude palm kernel oil.
Deodorising process : Remove odour and FFA from the bleach oil. The oil is heated and the vapour which is also know PFAD (palm fatty acid distillate) is remover from the oil. The palm oil and palm kernel oil are steamed at a temperature of 240°C to 260°C to get away the odors and tastes, and then they are cooled into room temperature (about 55°C) for further use. This process have great impact on the quality of the final palm oil and palm kernel oil.
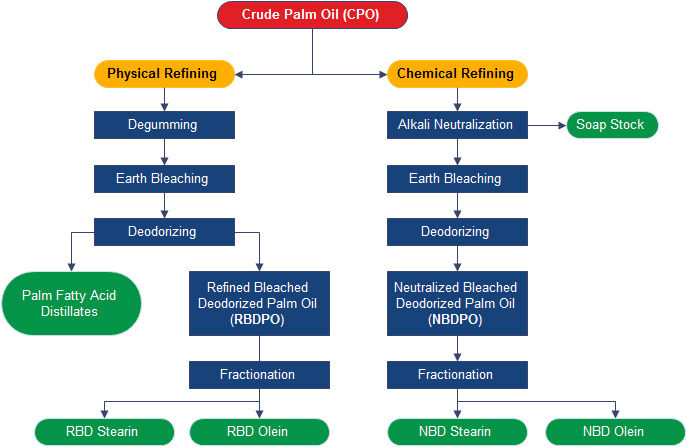
Refining Methods for Palm Oil Refining:
There are two refining methods for the palm oil refining in the palm oil refinery plant. They are physical refining and chemical refining. Physical refining means removing gum in palm oil during process of degumming in special method and removing FFA in process of deodorizing by steam. Chemical refining, however, means removing FFA in a chemical way (Acid-base neutralization). Gum and soap foot produced is separated by centrifuges.
Palm Oil Physical Refining Process
Oil physical refining process, also called as oil steam refining. During the degumming section in the palm oil milling plant, the gum will be removed from palm oil by utilizing phosphoric acid or citric acid. Next to bleaching section, the coloring matter and other metal ions will be absorbed or removed. Then, in the deacidification and and deodorization section, the crude palm oil will be processed within low pressure and high temperature. Through live stem, the FFA will be stripped of and the odors and colors will be removed or absorbed.
Palm Oil Chemical Refining Process
During the palm oil chemical refining process, the FFA will be removed and the neutralized crude palm oil and soap stock will be produced. And the soap stock will be separated from palm oil by using of high-speed separator. And the color pigments and the metal ions will be removed from the neutralized oil. If the crude palm oil contains high carotene, high FFA (more than 5% ) and relative low phosphatides, it will be great to have the chemical refining process to reduce the refining losses and the operation costs.
Different Outcome from Chemical and Physycal Refining Chemical Refining :
The finished oil is consistent and stable.
Excellent adaptability and less requirement to oil quality.
Less bleaching earth is added into compared with physical refining.
Physical Refining :
High oil refining rate, less oil loss.
No waste water discharged.
Especially suitable for oils of high acid value, and low gum content.
More FFA distilled out.
Equipment and Process Flow

Chempro Refining Design
THE NEUTRALIZATION PROCESS
Oil phase free of hydratable gums flows to a Centrifugal mixer after heating in a plate heat exchanger, where it is added with phosphoric acid from acid storage tank by a metering pump. The mixture is further taken to a Centrifugal mixer where it is added with caustic lye from lye solution service tank by a metering pump. The caustic solution circuit is completed with storage tank and recirculation pump. The mixture is then taken to a centrifuge where the non-hydratable gums and soap stock are separated and are pumped out of the system by a pump via a soap collecting tank. Washing : Oil free of gums and having traces of soapstock is pumped by a pump through a plate heat exchanger where it is heated by steam. Then it is sent to the Centrifugal mixer to be mixed with water and further centrifuged in a centrifuge for water washing. The washed water is then further sent to the slop oil tank for collection and recovery of escaped neutral oil which is then taken back to the system by a pump.
THE BLEACHING PROCESS
The unique CHEMPRO "SOFTBLEACH" bleaching system gently removes residual phosphatides, metals, soaps and oxidation products in addition to colouring matters. The feedstock is heated up in the Crude/Neutral Oil Economiser or Crude/Neutral Oil Heater to degumming or bleaching temperature. When there is a need for acid pretreatment, phosphoric acid is mixed vigorously with the oil in a Acid Mixer to ensure efficient mixing. The resultant mixture is than held in a Retention Tank to allow for the precipitation of gums before going to the Bleacher through the cascade vacuum dryer. When acid pre-treatment is not required , the feed stock is fed directly to the Bleacher after heating through the cascade vacuum dryer. Bleaching Earth and Activated carbon is added to the oil through a dosing unit which is controlled by PLC. The Bleacher is proprietary designed with internal partitions and set of high efficiency turbine agitators to avoid short cycling and provide necessary retention time before filtration. The conjunction of vacuum dryer with a Bleacher is what is unique about "SOFTBLEACH" whereby oil going to the Bleacher is thoroughly dried and deaerated in the cascade vacuum dryer besides the fugitive particles from the Bleacher are countercurrently scrubbed by the downcoming oil and hence bleaching earth going to the hotwell is avoided. The bleached oil from the Pressure Leaf Filters is transferred to the Bleached oil tank for intermediate storage.
THE DEODORIZATION PROCESS
The CHEMPRO "COMPACK DEODORISER" is based on thin-film, counter-current distillation technology which drastically reduces steam consumption less than half of what one would use in a conventional tray deodorizer. The COMPACK DEODORISER handles the most demanding of processing needs for a variety of stocks, in the most efficient manner besides being gentle on the oil. This ensures an extremely high steam to-oil interfacial surface without buildups or stagnant zones. Fatty acid removal occurs instantaneously and hydrolysis is avoided. Lower temperatures and lower residence times result in lower trans-fatty acid formation. The COMPACK DEODORISER is available in variants like single column and split column design whereby the packed column and tray column are in series or in parallel respectively. The advantage in the latter being flexibility to use only the tray column bypassing the packed column if need arises. Besides the other option available is final heating and cooling under vacuum . The superior scrubbing equipment featuring structured packing and strategically placed demisters ensures minimal carry-over of the fatty acid to the hot well.
May be usefull...
Adopt from some article
Comments