Manufacturing’s Next Act
- Andi Thoncianus
- Mar 23, 2018
- 5 min read
Industry 4.0 is more than just a flashy catchphrase. A confluence of trends and technologies promises to reshape the way things are made.
Mention “Industry 4.0” to most manufacturing executives and you will raise eyebrows. If they’ve heard of it, they are likely confused about what it is. If they haven’t heard of it, they’re likely to be skeptical of what they see as yet another piece of marketing hype, an empty catchphrase. And yet a closer look at what’s behind Industry 4.0 reveals some powerful emerging currents with strong potential to change the way factories work. It may be too much to say that it is another industrial revolution. But call it whatever you like; the fact is, Industry 4.0 is gathering force, and executives should carefully monitor the coming changes and develop strategies to take advantage of the new opportunities.
Start with some definitions. Industry 4.0 is the next phase in the digitization of the manufacturing sector, driven by four disruptions: the astonishing rise in data volumes, computational power, and connectivity, especially new low-power wide-area networks; the emergence of analytics and business-intelligence capabilities; new forms of human-machine interaction such as touch interfaces and augmented-reality systems; and improvements in transferring digital instructions to the physical world, such as advanced robotics and 3-D printing. (The four trends are not the reason for the “4.0,” however. Rather, this is the fourth major upheaval in modern manufacturing, following the lean revolution of the 1970s, the outsourcing phenomenon of the 1990s, and the automation that took off in the 2000s.)
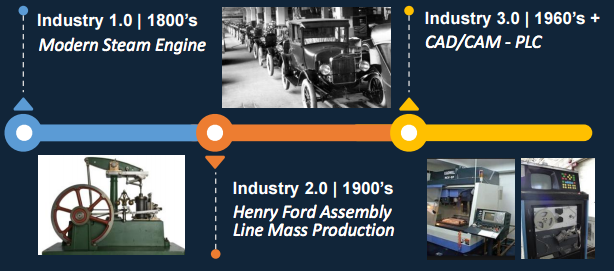
The first industrial revolution (1.0) involved the mechanization of production converting water to steam power. The second industrial revolution (2.0) took place 30 years later when the first electricity-powered assembly line introduced mass production. The third industrial revolution (3.0) started in the late 1960s when the first programmable logistic controller (PLC) enabled production automation through the use of electronic and IT systems.
Industry 4.0 refers to the combination of several major technology innovations, all maturing at the same time, that is expected to significantly shift the landscape of the manufacturing industry. These technologies – advanced robotics, artificial intelligence, sophisticated sensors, cloud computing and big data analytics – all exist in manufacturing today in some form, but as they integrate with one another, the physical and virtual worlds will interlink and transform the industry.
Advanced Manufacturing Technology
The key objective of Industry 4.0 is to drive manufacturing forward: to be faster, more efficient, and customer-centric while pushing beyond automation and optimization to discover new business opportunities and models.
By embedding modern technology into manufacturing, you essentially achieve Industry 4.0 objectives. In terms of business technology, it goes beyond transactions like accounts payable or receivable. It’s bigger than that. It goes beyond applications and software versions. Gone are the days of having to buy adapters and different layers of business technology to maintain and manage. And if the letters “ERP” make you cringe, it’s for good reason. ERP comes with a lot of administrative baggage and frankly dabbles in manufacturing. With the advent of cloud computing, there is a system that allows you to do more than just replace existing functionality. You can transform the way you do business and figure out how you’re going to beat the competition.
The other critical area where technology makes a big impact is with your workforce. Communication and collaboration are what will help you retain your best people. They need to talk about what is happening in the “manufacturing moment” to find the solutions that work. To attract quality candidates, you need to establish an environment that is similar to our everyday modern lives. The days of cubicles, tethered desktop computers, and physically being present on the shop floor are gone. Young workers want to run everything—including business—from mobile devices.
Stepping Stones to Industry 4.0
Cloud Computing. A single instance, multi-tenant environment scales with your business. Companies from startups to multinational global corporations are running on the same set of manufacturing software code and same database technology. This is the platform on which manufacturers need to build their Industry 4.0 environment.
Industrial Internet of Things (IIoT). Leading manufacturing companies are automatically receiving goods into the facility and the next thing a human does is drive the truck out the door -- which may be changing in upcoming years once vehicle automation is a reality. Everything in between receiving and shipping is done today through automation. It's all done through PLC integration and controls, which is highly efficient, higher product quality, and better customer satisfaction. IIoT connects devices from the shop floor and to ERP.
Agility and Sequencing. Similar to just-in-time (JIT) inventory strategy, sequencing is where components and parts arrive at a production line, in a specific configuration, at the exact time the product is required for the customer’s specific product configuration. This method of manufacturing will be a requirement for all manufacturing companies across the industry spectrum.
On-Demand Manufacturing. Consumer preference and demand patterns are starting to drive how the companies are going to be providing products to the market. In order to stay competitive, manufacturing companies need to be able to react and rapidly change the production process to align with the evolving demand patterns of its customer base. These variable demand patterns will be flowing through the enterprise business systems straight down to the shop floor manufacturing technology. The shop floor technology will then auto-configure the manufacturing production lines so the specific products can be manufactured. The days of large manufacturing plants making the same part or product,are gone. It's going to be localized manufacturing, supporting customers within a very specific region. You're going to need to be able to manufacture what the customer demands, based upon agility and sequencing.
The Digital Compass
With production data now available for the asking, executives rightly wonder about how to begin. Which data would be most beneficial? Which data leakages are causing the most pain? Which technologies would deliver the biggest return on investment for a company, given its unique circumstances? To sort through the choices, manufacturing leaders can use a “digital compass” (exhibit). The compass consists of eight basic value drivers and 26 practical Industry 4.0 levers. Cross-functional discussions that will help companies find the levers that are best suited to solve their particular problems.
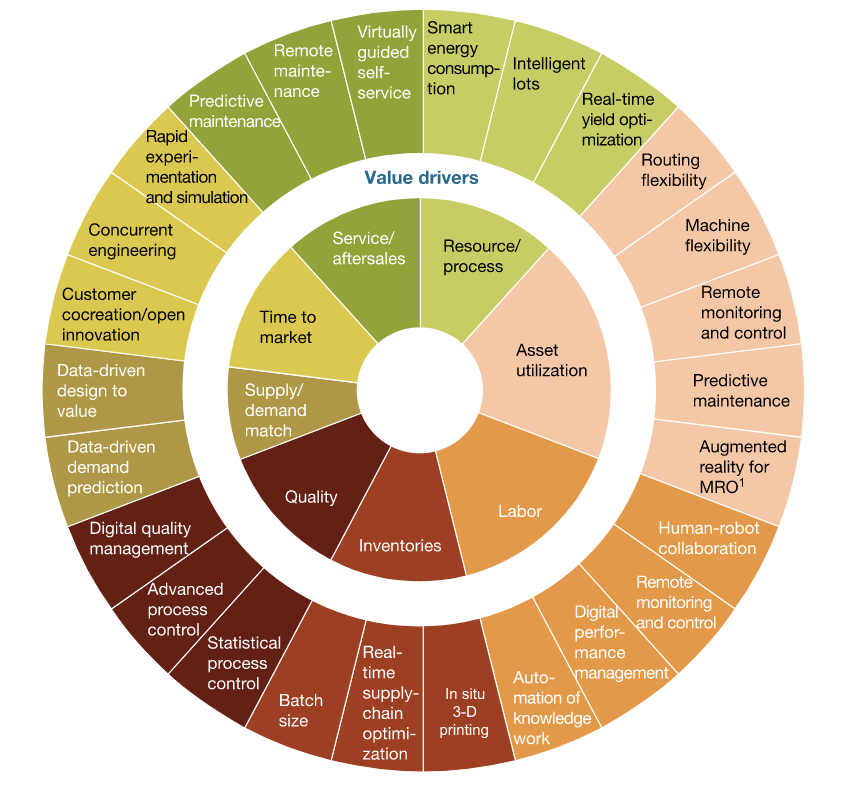
Stepping Stones to Industry 4.0
Cloud Computing. A single instance, multi-tenant environment scales with your business. Companies from startups to multinational global corporations are running on the same set of manufacturing software code and same database technology. This is the platform on which manufacturers need to build their Industry 4.0 environment.
Industrial Internet of Things (IIoT). Leading manufacturing companies are automatically receiving goods into the facility and the next thing a human does is drive the truck out the door -- which may be changing in upcoming years once vehicle automation is a reality. Everything in between receiving and shipping is done today through automation. It's all done through PLC integration and controls, which is highly efficient, higher product quality, and better customer satisfaction. IIoT connects devices from the shop floor and to ERP.
Agility and Sequencing. Similar to just-in-time (JIT) inventory strategy, sequencing is where components and parts arrive at a production line, in a specific configuration, at the exact time the product is required for the customer’s specific product configuration. This method of manufacturing will be a requirement for all manufacturing companies across the industry spectrum.
On-Demand Manufacturing. Consumer preference and demand patterns are starting to drive how the companies are going to be providing products to the market. In order to stay competitive, manufacturing companies need to be able to react and rapidly change the production process to align with the evolving demand patterns of its customer base. These variable demand patterns will be flowing through the enterprise business systems straight down to the shop floor manufacturing technology. The shop floor technology will then auto-configure the manufacturing production lines so the specific products can be manufactured. The days of large manufacturing plants making the same part or product,are gone. It's going to be localized manufacturing, supporting customers within a very specific region. You're going to need to be able to manufacture what the customer demands, based upon agility and sequencing.
Adopted from some article, may be useful...
Comments